Cogeneration- also known ascombined heat and poweror CHP - is the process of generating electricity and usable heat at the same time. The term has a modern, "green energy" ring to it, but cogeneration has been around since Edison's Pearl Street Station used heat from its turbines to warm the buildings of lower Manhattan in the 1880s. Cogeneration continues today because it makes sense to get as much benefit as possible from the energy you buy.
Generating electricity isn't always the first step in cogeneration. The process can start with capturing heat from furnaces and other high-temperature industrial processes, and using that heat to make steam that drives turbines to produce electricity.
Another technique involves recovering the combustible "waste" from lumber mills and sugar mills (or even the methane gas from sewage treatment plants) to fire boilers and help power facilities. The underlying principle is to maximize efficiency (and thus return on investment) by using as much of the available energy as possible. Facilities that produce large quantities of combustible material as a byproduct (pulp and sugar mills, for example) can generate additional revenue by selling excess electrical power. Additionally, tax incentives for adopting cogeneration and related energy-saving technologies are often available to defray costs.
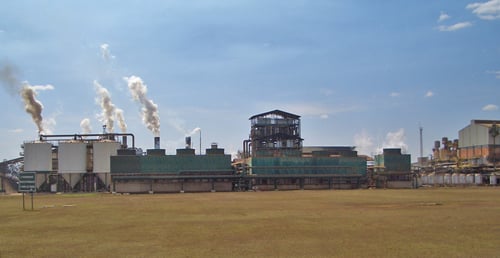
Who uses cogeneration?
Cogeneration is not just for large industrial facilities. Many smaller facilities, such as schools and hospitals, are using small-scale, self-contained cogeneration units to meet their electrical, heating, and cooling needs. Wherever a large amount of energy of any type is consumed, there may be an opportunity to use cogeneration.
What are the benefits of using cogeneration?
Reduced energy costs
With cogeneration, facilities that produce combustible materials as byproducts can exploit an essentially free fuel source for the price of a burner, boiler, and generator. Facilities that don't generate their own fuel can often purchase natural gas for cogeneration use at reduced rates. Cogeneration can reduce energy costs by as much as 40 percent, according to some estimates.
Increased power reliability and better return on investment
Emergency power systems are required where human life would be endangered by an outage, such as at airports and hospitals, but backup generators represent a substantial investment that produces nothing in return while standing idle. A self-contained cogeneration system is similar to a backup generator system, but with a much higher return on investment. With a properly sized cogeneration unit, all electrical needs can be met on-site, and the utility grid becomes the backup source of electrical power.
Reduced environmental impact
Maximizing fuel efficiency lowers greenhouse gas emissions. When waste heat is recovered, less fuel is needed to produce the required energy. For example, a hospital with a modern combined heat and power plant that provides 100 percent of its own electrical power does not need to burn additional fuel to fire its boilers, and uses virtually no electricity for its chillers. According to one of the nation's leading cogeneration engineering, construction, and consulting firms, a cogeneration plant at such a facility may use as much as 250 percent less fossil fuel than if supplied from a traditional utility plant.
How do I decide if cogeneration is right for my facility?
There are many factors to consider when deciding on cogeneration. Construction costs for cogeneration units can be higher than building traditional power plants for large facilities. In addition to construction costs, maintenance costs must be considered.
Consultants who specialize in cogeneration should be brought in as part of the planning process. Cogeneration equipment suppliers can also be an excellent source of information, and the US Department of Energy's Advanced Manufacturing Office (AMO) program can provide technical assistance.
When to consider adding cogeneration
- Cogeneration equipment can be installed at any time, but during the design phase is ideal.
- A heat-recovery boiler may be a cost-effective replacement for an old boiler.
- If your facility requires increased power reliability.
- If your organization wants to increase energy efficiency and reduce environmental impact.
Cogeneration checklist
To help determine the feasibility of cogeneration for your facility, here are some questions to consider:
- How much energy is consumed by your electrical, heating, and cooling equipment? (Answering this question will probably require a detailed energy audit.)
- If your heating and cooling equipment is old and you are considering replacement or refurbishment, it may be the right time to add cogeneration.
- What is the cost of the electric energy you are replacing?
- What tax credits or other funds are available? Investment and electric power production tax credits may be available for your facility. Also, the American Recovery and Reinvestment Act (ARRA) is providing $256 million for industrial energy efficiency related projects, including cogeneration.
- Does your facility produce methane gas, landfill gases, or biofuels as a byproduct?
- What will you pay for natural gas if it is your only source for heating fuel? Consult cogeneration equipment suppliers to consider other fuel supplies and to compare costs
- How much energy is consumed by your electrical, heating, and cooling equipment? (Answering this question will probably require a detailed energy audit.)
- If your heating and cooling equipment is old and you are considering replacement or refurbishment, it may be the right time to add cogeneration.
- What is the cost of the electric energy you are replacing?
- What tax credits or other funds available? Investment and electric power production tax credits may be available for your facility. Also, the American Recovery and Reinvestment Act (ARRA) is providing $256 million for industrial energy efficiency related projects, including cogeneration
- Does your facility produce methane gas, landfill gases, or biofuels as a byproduct?
- What will you pay for natural gas if it is your only source for heating fuel? Consult cogeneration equipment suppliers to consider other fuel supplies and to compare costs.
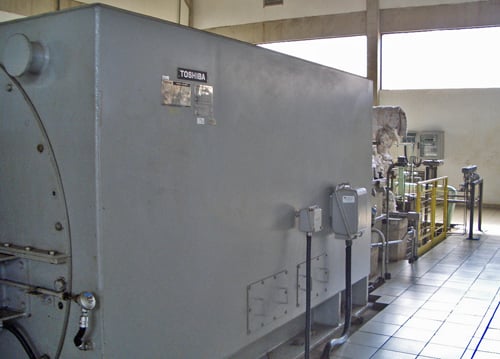
Properly designed, installed, and maintained cogeneration operations can save your facility money, reduce environmental impact, and provide a reliable source of energy - but careful planning is required. To make the right choice, you must know your heating, cooling, and electric energy requirements, and understand the cogeneration process and the options available.
Resources
To find data, visit the United States Department of Energy's Industrial Distributed Energy website.
- "Advanced Manufacturing Office (AMO)" at the US Department of Energy's "Energy Efficiency & Renewable Energy" web site
- Rich McKown, PE, "Combined Heat and Power: Reaping the Benefits of Changed Market Conditions," Burns & McDonnell white paper, 2009
- Funding Opportunities at the US Department of Energy's "Energy Efficiency and Renewable Energy" web site