Vibration is simply a back and forth movement—or oscillation—of machines and components in motorized equipment. Vibration in industrial equipment can be a symptom, or cause, of a problem, or it can be associated with normal operation. For example, oscillating sanders and vibratory tumblers rely on vibration to function. Internal combustion engines and gear drives, on the other hand, experience a certain amount of unavoidable vibration.
For the most part, mechanical equipment is engineered to avoid vibration rather than produce it. This article focuses on equipment engineered to avoid vibration.
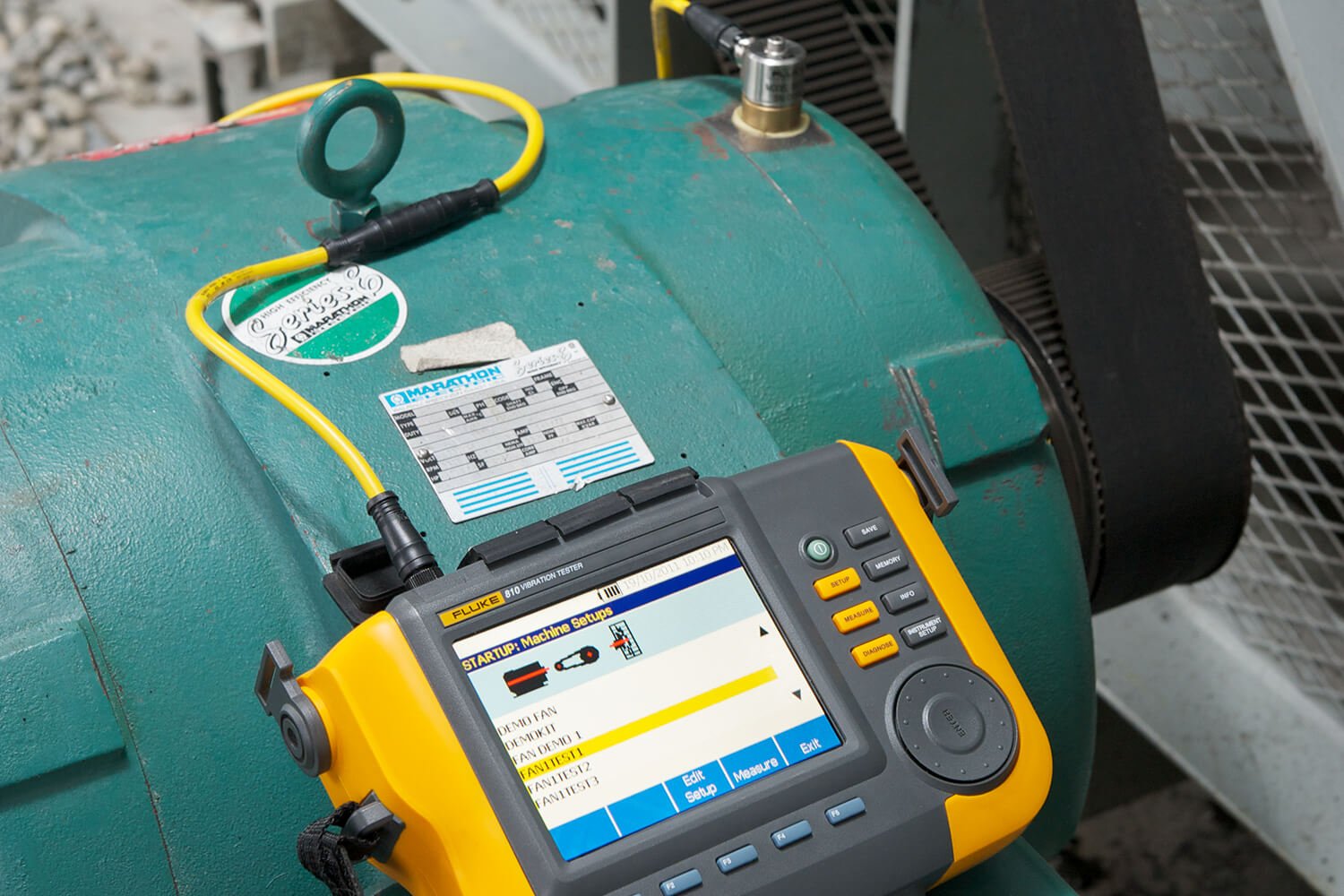
Vibration can indicate a problem and if left unchecked can cause damage or expedited deterioration. Vibration can be caused by one or more factors at any given time, the most common being imbalance, misalignment, wear and looseness.
- Imbalance - A "heavy spot" in a rotating component will cause vibration when the unbalanced weight rotates around the machine's axis, creating a centrifugal force. Imbalance could be caused by manufacturing defects (machining errors, casting flaws) or maintenance issues (deformed or dirty fan blades, missing balance weights). As machine speed increases the effects of imbalance become greater. Imbalance can severely reduce bearing life as well as cause undue machine vibration.
- Misalignment /shaft runout - Vibration can result when machine shafts are out of line. Angular misalignment occurs when the axes of (for example) a motor and pump are not parallel. When the axes are parallel but not exactly aligned, the condition is known as parallel misalignment. Misalignment can be caused during assembly or develop over time, due to thermal expansion, components shifting or improper reassembly after maintenance. The resulting vibration can be radial or axial (in line with the axis of the machine) or both.
- Wear - As components such as ball or roller bearings, drive belts or gears become worn, they might cause vibration. When a roller bearing race becomes pitted, for instance, the bearing rollers will cause a vibration each time they travel over the damaged area. A gear tooth that is heavily chipped or worn, or a drive belt that is breaking down, can also produce vibration.
- Looseness - Vibration that might otherwise go unnoticed can become obvious and destructive if the component that is vibrating has loose bearings or is loosely attached to its mounts. Such looseness might or might not be caused by the underlying vibration. Whatever its cause, looseness can allow any vibration present to cause damage, such as further bearing wear, wear and fatigue in equipment mounts and other components.
Vibration effects
Vibration can accelerate machine wear, consume excess power, and cause equipment to be taken out of service, resulting in unplanned downtime. Other effects of vibration include safety issues and diminished working conditions. When measured and analyzed properly, however, vibration can play an important role in preventive maintenance programs. It can serve as an indicator of machine condition and allow plant maintenance professionals to act before damage or disaster strike.
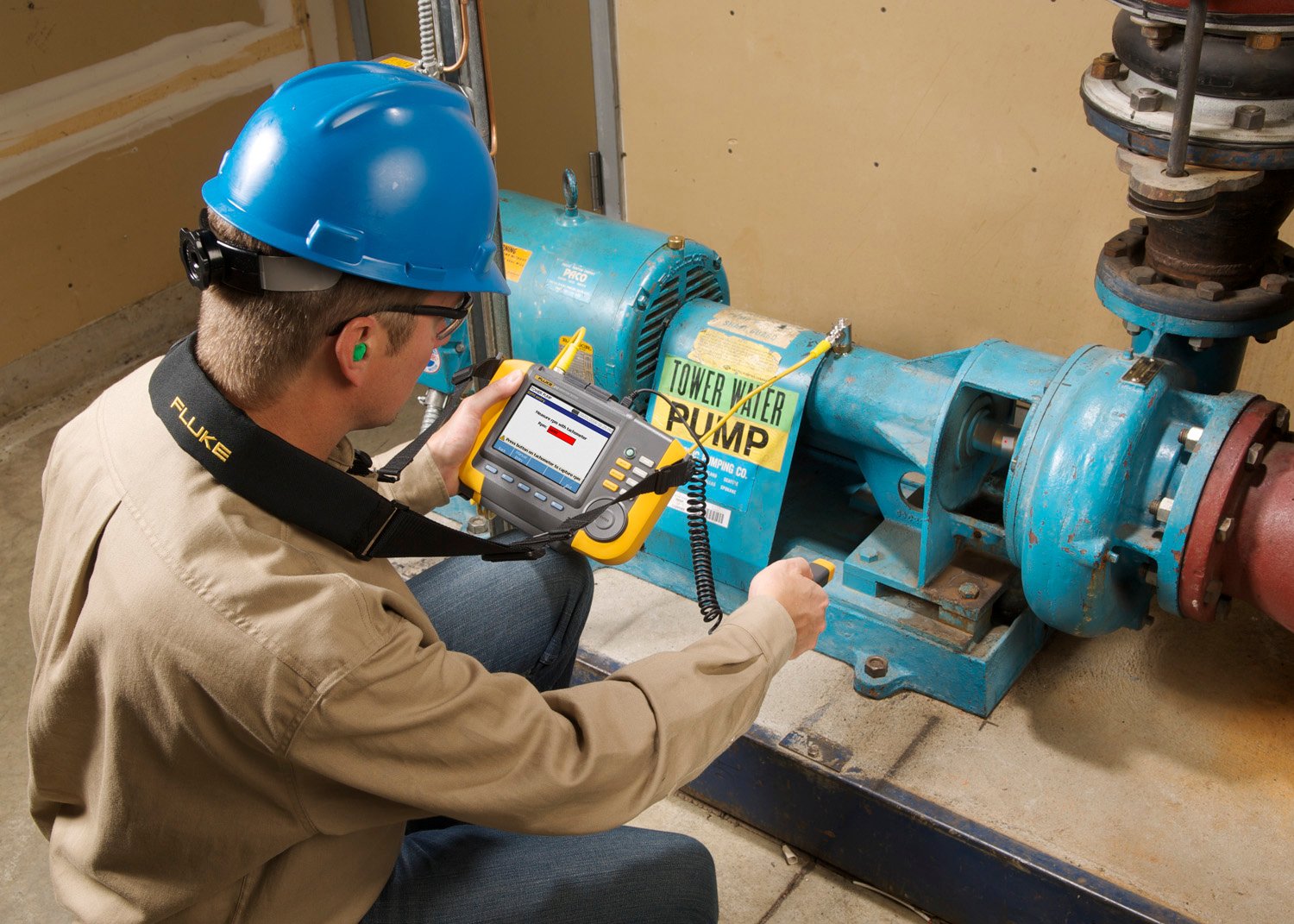
Consider these variables when analyzing vibration:
- Direction, such as radial or axial
- Amplitude, severity
- Frequency, expressed in cycles per minute (CPM) or Hertz (Hz)—one Hz equals one second, or 60 CPM
Plant maintenance technicians need to be able to differentiate between normal and abnormal vibration. A good understanding of vibration basics and the right tool is all a plant maintenance technician needs to quickly and reliably get to the bottom of vibration-related issues, including finding the root cause and severity, then determining the need for service or repair.
The Fluke 810 Vibration Tester
Vibration testers and software are typically designed for monitoring machine condition over the long term and can be expensive and require special training. Many industrial maintenance teams operate with strict limits on their budgets and time; the resources required for the training and implementation associated with long-term vibration analysis programs may simply be out of reach. This is where the Fluke 810 steps in and one reason why it is such a valuable tool.
The Fluke 810 Handheld Vibration Tester is designed to help maintenance professionals determine machine condition and get to the root cause of any problems quickly. It fills the gap that exists between high-end, complex vibration analyzers and low-end vibration pens, which sacrifice accuracy for cost and ease of use. The Fluke 810 offers the diagnostic capabilities of the higher-end analyzers along with the speed and convenience of the lower-end testers, at a reasonable price.
The Fluke 810 is engineered and programmed to:
- Discover and diagnose common mechanical problems
- Detect vibration along three planes (vertical, horizontal and axial)
- Provide plain-text diagnoses with recommended solutions, including imbalance, misalignment, wear, and more
- Test a wide range of mechanical equipment, including motors, fans, blowers, drives, gearboxes, couplings, pumps, compressors and spindles
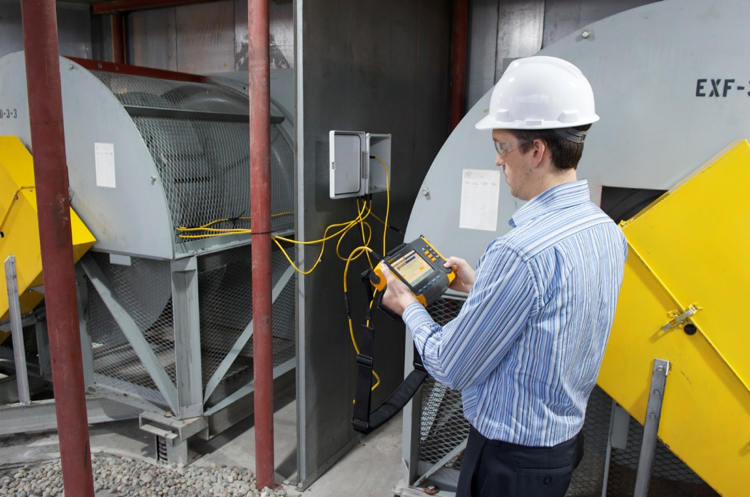
Plant maintenance technicians need comprehensive diagnostic and problem-solving tools to identify problems, recommend repairs and give context-sensitive guidance and tips in real time. The precision of the Fluke 810 allows maintenance teams to act when needed to keep mechanical equipment in peak condition, and to keep facilities productive.