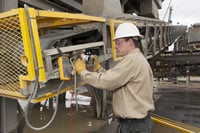
Auf der Baustelle stehen Betonfertiger bereit, um aus der fertigen nassen Materialmischung einen neuen Autobahnabschnitt zu bilden. Transportmischer stehen an der Betonmischanlage an und warten auf ihre Ladungen. Aber der Betrieb steht aufgrund eines elektrischen Problems still. Zeit, bei Keithly Electric anzurufen.
Dutzende Arbeiter, Fahrer und Autobahnarbeiter warten darauf, dass sich die Mischung in Bewegung setzt. Der Druck, das Produkt erneut in Gang zu setzen, ist also sehr hoch. Jeder stellt sich also die Frage: Wie lange dauert es, bis der Fehler behoben ist?
„Das ist die erste Frage, die Sie hören, wenn Sie aus Ihrem EinsatzwagenLkw aussteigen“, sagt Greg Burdick, Elektriker und Programmierer bei Keithly. Beim entsprechenden Druck und angesichts der Erkenntnis, dass Zeit Geld ist, weiß man bei Keithly sehr genau, dass erfahrene Leute mit vielen verschiedenen Kompetenzen, die den Betrieb schnell wieder ans Laufen bringen, der Schlüssel zum Erfolg sind.
Seit der Gründung des Unternehmens durch Bob Keithly im Jahr 1967 hat Keithly Electric stets größten Wert auf enge Beziehungen zu Kunden und Mitarbeitern gelegt. Heute sind die 35 Mitarbeiter im gesamten Großraum Seattle im Einsatz – auf Schiffen mit und ohne eigenen Antrieb, auf Kranen, Binnenschiffen, in Gebäuden und Wohnhäusern, in Lebensmittel- und Luft- und Raumfahrtsanlagen. Sie konstruieren und warten alles von alltäglichen Stromkreisen und Drähten bis hin zu komplexen Systemen mit speicherprogrammierbaren Steuerungen (SPS). Seit dem Start hat das Unternehmen viele Beton-, Asphalt- und Bau- und Aggregatvorgänge am Laufen gehalten.
Echter BissTrue Grit
Materialverarbeitende Betriebe haben ständig mit Gefahren zu kämpfen, die die Geräte zum Stillstand bringen können: Alles wird mit Staub und Schotter überdeckt und das Wasser zum Waschen des Kies spritztfließt in die Baukonstruktion und in den Boden. Diese Betriebe laufen schnell und mit schlanken Prozessen – es gibt kein Ersatzkontingent, das bei Anhalten des Betriebs aufgrund elektrischer Probleme aktiviert werden kann. Wenn Herr Burdick vor Ort eintrifft, weiß er also, dass es für die zuständigen Leiter ganz entscheidend ist, den Betrieb schnellstmöglich wieder aufzunehmen. Am Arbeitsplatz herrschen harte Bedingungen, aber Greg Burdick ist ein harter Kerl.
Er hat schon viel größere Herausforderungen gemeistert als die Probleme in dieser schwierigen Umgebung. Vor einigen Jahren kam er durch eine Infektion mit fleischfressenden Bakterien (nekrotisierende Faszitis) fast ums Leben. Dabei verlor er sein linkes Bein unterhalb des Knies und einen Teil seinesn rechten Fuß. Er verlor jedoch nicht seinen Sinn für Humor.
„Dieses Persönlichkeitsmerkmal gehört nicht wirklich zur Arbeit dazu“, sagt er und lacht. Er kam zur Arbeit zurück, nachdem eine Untersuchung ergab, dass er zu „allem noch so erdenklich Furchtbaren, was ein Elektriker unter Umständen tun muss“ in der Lage sei.
Burdick beschränkt sich nicht darauf, Defekte zu beheben. Burdick und das Team von Keithly arbeiten auch Hand in Hand mit den Betriebsleitern, um Betriebssysteme neu zu konstruieren und zu automatisieren, um so für mehr Effizienz und Zuverlässigkeit zu sorgen. Die von Keithly konzipierten und konstruierten SPS-Systeme dienen dem Anschluss und der Steuerung von Antrieben mit variabler Frequenz (VFDs), Sensoren, Alarmen und weiteren Elementen. Mithilfe von Touchscreen-Displays kann ein einziger Bediener einen ganzen Betrieb steuern.
Einer dieser Kunden ist ein riesiger Betrieb mit einer Fläche von ca. 200 Ha, ein regionaler Lieferant von Zuschlagstoffen, Splitten und Asphalt.
Hinter dem Asphaltverarbeitungswert und dem Hauptbüro und den Waagen befindet sich das Materialwerk, ein Komplex aus Brechern, ineinandergreifenden Förderbändern, Sortiersieben und Waschanlagen, die an eine coole Achterbahn erinnern.
In der Ferne befinden sich Hügel aus Felsbrocken und Steinaufschüttungen und die Gruben, in denen sich Sand, Kies und Steine durch die Gletscher aus der Eiszeit angelagert haben, die auf 100-Tonnen-Kappschaufel-Muldenkipper verladen werden. Mit diesen Lkws werden die Ladungen dann zu den Gittersieben gefahren. Dort werden mit einer Reihe starker paralleler Balken große Felsen und andere Rückstände von Materialien geringerer Größe getrennt. Sand, Kies und kleines Gestein werden durchgelassen und fallen auf ein Förderband, über das sie durch Kegelbrecher, weitere Förderbänder, Sortiersiebe und Waschanlagen geleitet werden. Größere Teile, d. h. Felsen mit einem Durchmesser von über 1,20 m fallen in eine Grube, um von dort zu einem Balkenbrecher befördert zu werden.
Bei einem Besuch am Werk sieht man, dass zum Brechen von Gestein mehr erforderlich ist als rohe Gewalt. Damit Gestein sich nicht anstaut und alles blockiert, müssen die Gitter immer nach einigen Lkw-Ladungen geleert werden. Früher mussten die Lkw-Fahrer eine Taste betätigen, um jede Ladung einzeln zu registrieren.
Keithly hatte da eine bessere Idee. Burdick befestigte Induktionsschleifen an den Siebgittern, um die Ankunft und Abfahrt der Muldenkipper zu erfassen. Die Schleifen waren ursprünglich zur Befestigung unter dem Straßenbelag vorgesehen, um Autos zu erfassen, die vor einer Ampel warteten. Durch die Schleifensignale erhält das Steuerungssystem jetzt die Nachricht, wie viele Ladungen an jedes Siebgitter gelangt sind sowie eine Bestätigung, dass die Muldenkipper abgefahren sind und die Siebgitter geleert werden können. Über ein SPS-Schaltfeld in der Nähe der Siebgitter erhält man eine Übersicht über den Vorgang
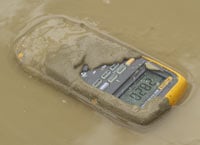
Eine bessere Lösung finden
Der Schleifensiebsensor ist Teil eines neu konzipierten Steuersystems, das Keithly vor Kurzem für das Werken Betrieb angefertigt hat. Der Bediener erhält jetzt über einen Touchscreen eine graphische Übersicht über das gesamte Werk mit seinen verschiedenen Verteilern, Förderbändern und Brechern. Die Status aller Motoren, Sortierer und Pumpen und der Ladestand in jedem Materialsilo sind auf Anzeigen zu erkennen. Das Ergebnis: Das automatisierte System erfasst Probleme wie z. B. Materialüberschuss, sodass die Bediener informiert werden, bevor echte Probleme entstehen. So steigt die Produktion und die Betriebskosten sinken.
Wenn Störmeldungen eintreffen und der Druck steigt, behält Burdick den Prozess im Auge. „Es geht eigentlich nur darum, so gründlich und methodisch genau wie möglich vorzugehen – es geht nur um Fehlersuche.“, so Burdick. „Man muss nicht alle Details des Systems kennen, aber man muss genug über die Komponenten wissen, um einen Startpunkt zu finden. Manchmal muss man dann im weiteren Verlauf die Puzzleteile zusammenfügen.“
Dieser Prozess kann so gut wie jeden Elektrotest umfassen, den es gibt – von einfachen Spannungs-, Strom- und Erdungsprüfungen bis zur Fehlersuche bei den immer häufiger verwendeten VFDs. „Ich teste oft Antriebe, und der Test des vorderen und hinteren Antriebsendes – dier Leistungseinheit – ist im Wesentlichen ein Diodentest“, so Burdick. „Der Diodentest ist eine Funktion des Multimeters – damit wird die Spannung gemessen, die erforderlich wäre, um eine Diode in Brand zu setzen.“
Burdick prüft ebenso die synthetische Frequenz der VFDs mit der Funktion, die sich auf einigen Fluke Digitalmultimetern befindet. „Mein neues Messgerät, das Fluke 28 II, hat einen Tiefpassfilter zur Prüfung von Antrieben mit regelbarer Drehzahl. Ich habe es verwendet, um zu prüfen, ob die Anzeige auf dem Antrieb stimmt“, sagt Burdick.
Das Multimeter Fluke 28 II mit IP67-Spezifikation für wasser- und staubdichten Schutz und Stürze aus drei Metern Höhe wurde speziell für Arbeiten unter den widrigen Bedingungen entwickelt, mit denen es Burdick zu tun hat.
„Die Sturzfestigkeit zahlt sich meist im Zusammenhang mit Leitern aus“, sagt Burdick und lacht. „Immer, wenn man in großer Höhe arbeitet, besteht die Gefahr, dass die Leiter wackelt und man das Gerät fallen lässt. Am besten verwendet man hier den Magnetsatz (das magnetische Fluke-Kit zum Aufhängen des Multimeters ToolPak™).“
Zum Thema Wasser.
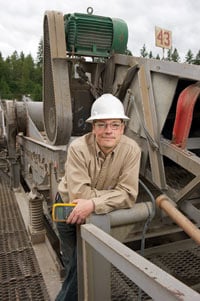
Das Feuchtigkeitsproblem
„Einmal habe ich mein gutes altes Messgerät fast ruiniert“, so Burdick. „Ich ging durch den Regen von einem Schaltfeld zum Kontrollhaus. Als ich am Kontrollhaus angekommen war, um das andere Ende des Stromkreises zu überprüfen, war der Drehschalter schon mit Wasser gefüllt, da ich das Messgerät mit der Anzeige nach oben gehalten hatte.“
Und mit dem Fluke 28 II? Burdick: „Ich denke nicht einmal mehr darüber nach“. „Ich habe das 28 II 2009 auf der Rockwell Automation Fair in Kalifornien in einem Wassertank gesehen. Da habe ich mir gleich gesagt: Das ist das richtige für mich.“
Für Arbeiten an Schaltschränken verwendet Burdick die Multimeter Fluke 28 II und Fluke 189. „Bei niedriger Spannung, also in der Regel bei Gleichstromsignalen und bei Strommessungen, setze ich eher auf das Fluke 189“, weiß Burdick zu berichten. „Für Analogsignale verwende ich auch oft die Milliampere-Strommesszange Fluke 771. Man muss nicht in den Stromkreis eindringen, um einen Messwert zu erhalten. Ich habe kaum Unterschiede zwischen diesen Messungen und solchen feststellen können, die man erhält, wenn man in den Stromkreis eingreift und diesen durch ein Messgerät führen lässt.
Zum Prüfen von Antriebssteuerungs-Schaltschränken verwendet Burdick ein älteres Isolationswiderstandsmessgerät, das Fluke 1520. „Bei den meisten Lasten unserer Kunden geht es um Motorlasten“, so Burdick. „Ich nutze es immerdie gesamte Zeit, um zu prüfen, ob ein Motor defekt ist oder ein Kabel kurzgeschlossen ist.“
Die Erdung von Geräten ist ein weiterer wichtiger zu berücksichtigender Aspekt. Materialverarbeitende Betriebe richten sich nach den Vorschriften der MSHA (Mine Safety and Health Administration) in den USA, die strenge Anforderungen an die Erdung umfassen. „Es gibt ein Erdungsabsicherungsprogramm“, weiß Burdick. „Alle Betriebe müssen jährlich geprüft werden und jeder Motor muss auf Erdschluss geprüft werden. Wenn ich eine dieser Aufgaben zu erledigen habe, verwende ich das Fluke 1520 bei niederohmigen Messwerten.
„Wenn der Motor kurzgeschlossen wird und die Drähte aus dem Verteilerkasten herausragen, muss ein Pfad mit niedrigem Widerstand zur Erde vorhanden sein, um den AusschalterLeistungsschalter zu aktivieren. Ich habe schon Stellen gesehen, an denen die Erde nicht durchgehend war und kein funktionsfähiger Pfad zurück zu den Erdstäben des Systems vorhanden war. Bei einer Fehlerbedingung wird die Gebäudestruktur unter Spannung gesetzt. Wenn man bei 480-Volt-Motoren an das Geländer fasst und dabei in einer Wasserpfütze steht, kann das sehr ungemütlich sein.“
Extraleistung ist gefragtDen längeren Weg gehen
Manchmal muss man im Kundendienst einfach Extraleistung erbringenden längeren Weg gehen. Eines Tages meldete eine Betonmischanlage, dass der große Trommelmischer – die Einheit, die zum Füllen der Fahrmischer gekippt wird – nicht richtig funktionierte. Der Kippmechanismus, der normalerweise bei regelbarer Drehzahl zur Abfederung des Stoßes beim Bewegen des schweren Gefäßes aktiv wurde, lief nur mitbei einer Drehzahl. Der Betrieb konnte nicht abgeschaltet werden, daher musste der Test am laufenden System erfolgen.
Mithilfe seines Fluke 189 Multimeters konnte Burdick die Ursache auf das Steuerungsmodul eingrenzen.
„Das Steuerungsmodul sendete kein GleichstromsDC-Signal (DC) mehr. Und das haben wir nur daran erkannt, dass beim Einhaken des Messgeräts an der Ausgangsklemme sich das analoge Balkendiagramm auf dem Messgerät hin- und herbewegte“, sagte er.
„Ein DC-Signal, so viel steht fest. Aber irgendetwas stimmte mit dem Steuerungsmodul nicht, das das DC-Signal abgab. Es sprang im Bereich von zwei bis acht Volt ständig hin und her. Am Ventil kam ein Durchschnittswert des Signals an. Das Steuerungsmodul war einfach kaputt.“
Das defekte Steuerungsmodul musste mithilfe eines Spezialanschlusses ausgetauscht werden, ohne den Betrieb für zwei Tage stillzulegen. Dan Keithly kannte eine andere Betonmischanlage, die über die gleichen Steuerungen verfügte und nicht in Betrieb war. Er kontaktierte den Besitzer, und vereinbarte, das Modul auszuleihen. Er war zweieinhalb Stunden unterwegs, um das Ersatzmodul zu beschaffen.
Aber die Zeit war sinnvoll investiert. Der Kunde konnte den Betrieb aufrechterhalten. Und das ist für Keithly Electric das A und O.