In der warmen Sommersaison arbeiten Kühlanlagen nahezu mit Spitzenleistung. Wenn die Anlage für kritische Gebäudefunktionen verwendet wird, ist jede Ausfallzeit, aus welchem Grund auch immer, inakzeptabel.
Ganz besonders empfindlich sind Krankenhäuser, die sich auf ihre zentralen Kühlsysteme in Pflegebereichen für schwerkranke Patienten verlassen können müssen, z. B. in Operationssälen und Notaufnahmen. Wenn keine Kühlung mehr möglich ist, können unzureichende Umgebungsbedingungen die Gesundheit der Patienten bedrohen oder verhindern, dass Operationen stattfinden und so mögliche Haftungsansprüche schaffen.
Eine häufiger vorkommende Situation sind die vielen gewerbliche und Leichtindustrie-Gebäude, die heute Rechenzentren mit zahlreichen Servern im Haus haben. Diese Server könnten vor kritische Daten verantwortlich sein, beispielsweise personenbezogene Daten, Echtzeit-Finanztransaktionen oder Flugtickets. Auch diese Server erzeugen große Mengen an Wärme, die entweder abgeleitet oder mit kühler Luft ausgeglichen werden müssen. Ein Verlust der Kühlwasser-Kühlkapazität, auch wenn er nur wenige Minuten andauert, kann dazu führen, dass ein Serverraum abgeschaltet wird. In der großen Mehrheit von Krankenhäusern von Rechenzentren wird die Kühlung durch eine Reihe von Wasserkühlern, Pumpen und Kühltürmen erreicht. Die Wasserkühler können mit Zentrifugal-, Schrauben- oder Scrollverdichtern ausgestattet sein. Meist liefert eine Reihe von Zentrifugalverdichtern Redundanz und stufenweise Kapazität.
Kühler, Pumpen und Kühlturmlüfter nutzen alle Dreiphasen-Motoren, um Wasser zu bewegen, Luft zu bewegen oder Kühlmittel zu komprimieren. Der Ausfall einer dieser Motoren kann den Betrieb des gesamten Kühlsystems bedrohen. Es ist sehr wichtig, dass ALLE Motoren gründlich geprüft werden, bevor sie für die Kühlsaison in Betrieb genommen werden. Auch wenn ein Notdienst für dies Geräte verfügbar ist, so ist dieser doch enorm teuer. Stundensätze von 250 $ pro Person in der Nacht und an Wochenende sind keine Seltenheit, und hinzu kommen hohe zusätzliche Kosten für Transport und Teile.
Auch wenn es eine Reihe von Diagnoseprüfungen gibt, die vor der Inbetriebnahme zu Saisonbeginn durchgeführt werden können und sollten, ist nichts wichtiger als eine Prüfung des Motorwiderstands mit einem Isolationsmessgerät. Das Isolationsmessgerät schaltet eine hohe Spannung auf die einzelnen Motorwicklungen auf und misst dabei den Wicklungswiderstand. Ein geringer Widerstand bedeutet, dass die Wicklung Verschleiß aufweist und nach Inbetriebnahme des Geräts ausfallen könnte.
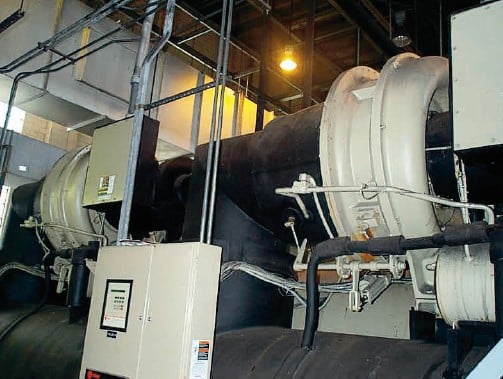
Im Allgemeinen gelten für die Verwendung eines Isolationsmessgeräts die folgenden Schritte:
- Tragen Sie persönliche Schutzausrüstung und halten Sie jederzeit die Sicherheitsbestimmungen ein. Schützen Sie Ihre Augen mit einer Schutzbrille. Trennen Sie den Motor von allen Stromquellen, bevor Sie den Versuch einer Reparatur unternehmen. Befolgen Sie Prozeduren zur Kennzeichnung und zur Sicherung gegen das Wiedereinschalten. Prüfen Sie noch einmal mit dem Multimeter, dass auch wirklich die gesamte Stromversorgung getrennt ist.
- Entfernen Sie die Schrauben, die die Kabelanschlussabdeckung sichern, vom Motor, und legen Sie sie beiseite. Lösen Sie die Versorgungskabel von den Motorleitungen; Sie müssen möglicherweise die Paare mit Etiketten oder Nummern kennzeichnen, damit Sie die richtige Rotation beibehalten können, insbesondere bei Dreiphasen-Motoren. Normalerweise muss das Gerät mindestens 24 Stunden lang bei Raumtemperatur stehen, bevor Sie die Prüfung durchführen können. Stellen Sie auch sicher, dass sich der Motor nicht in einem Vakuum befindet, wenn die Isolationsprüfung durchgeführt, da das den Motor zerstören könnte.
Die Isolierung und die Wicklungen der Kühlturmlüftermotoren müssen getestet werden. - Verbinden Sie eine Leitung des Isolationsmessgeräts mit einer der Motorleitungen und die andere mit der Motorerdung oder dem Metallgehäuse. Schalten Sie das Messgerät ein oder drehen Sie am Griff. Der Hersteller des Messgeräts sollte über Referenzmesswerte für jedes Messgerät verfügen. Im Allgemeinen sollte ein Messwert über 20 bis 30 Megaohm ausreichend für den Betrieb der meisten Motoren sein. Alle neuen Motoren sollten Messwerte von über 999 Megaohm zeigen; Messwerte darunter bedeuten, dass eine Verschlechterung der Wicklungsisolation vorliegt.
- Prüfen Sie die einzelnen Motorwicklungen nacheinander und zeichnen Sie die Megaohm-Werte für jeden Satz von Wicklungen auf. Hochwertigere Isolationsmessgeräte bieten die Möglichkeit, die Daten zur späteren Verwendung auf einem Laptop zu protokollieren. Wenn einer der Stränge einen sehr niedrigen Messwert aufweist, sollte der Motor ausgetauscht werden. Dies führt auch zur Aufnahme einer hohen Stromstärke oder ständig durchgebrannten Sicherungen. Viele Hersteller stellen eine Tabelle mit den korrekten Messwerten bereit.
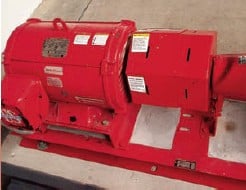
Beachten Sie wie immer alle Empfehlungen zur Verwendung des Geräte- und des Messgeräteherstellers.
Welche Motoren in einer Kühlanlage sollten geprüft werden? Die Antwort lautet: alle Motoren oder so viele Motoren wie möglich. Dazu gehören natürlich mindestens die Kühler- und Pumpenmotoren. Außerdem sollten der Motor der Kühlerölpumpe und die Motoren der Kühlturmlüfter geprüft werden. Wenn einer dieser Motoren ausfällt, könnte das zur Folge haben, dass die gesamte Kühlanlage ausfällt.
Grundsätzlich gilt, dass durch Isolationsprüfungen am Motor Probleme so rechtzeitig erkannt werden können, dass sie behoben werden können, während dies noch möglich ist.